Lubricants For Mac
Water based rubber lubricant emulsion of a fluorochemical/ resin mixture. Provides a dry, colorless film with a very low coefficient of friction and excellent lubricating properties. Intended for use as a lubricant on rubber, plastic and metal parts. Typical Applications:. Assembly Aid,. Gaskets,.
Hose,. Insertion Aid,.
O-Rings,. Seals,. Tubes,.
Window & Door Seals Materials:. All Metal Surfaces,. Rubber,. Plastic,.
Composite Available in:. Gallon Container,. 5 Gallon Pail,.
55 Gallon Drum,. 275 Gallon Totes.
IndiaMART Member Since May 2005 The McLube Division of McGee Industries, Inc. Has been manufacturing high-technology mold releases and industrial lubricants since 1954.
Our products include water and solvent- based release and antitack coatings and a full line of oils, greases and dry film lubricants. Through six decades of innovation, McLube products have earned an international reputation for performance and McLube people have earned world wide industry recognition as expert problem solvers. At McLube, we’re specialists in assessing complex processes and unusual conditions- and developing solutions that work. We’re experienced in solving problems for a broad industrial base, from manufacturers of rubber and plastic goods to producers of insulation and composite materials, including those used in marine and aerospace applications. Team McLube technical experts work closely with our customers to obtain optimal performance with our standard products - and to develop special formulations to meet your unique process requirements. All with fast turn-around. And as we develop release and lubrication technology to meet today’s needs, we are actively engaged in researching and developing new technologies for the future.
For technical assistance in selecting the appropriate McLube product, evaluating a McLube product under your operating conditions, or developing special formulations for your process: Simply call 1-800-2-MCLUBE (1-800-262-5823). An unwavering commitment to technical leadership and outstanding service.
A lubricant is a substance, usually organic, introduced to reduce friction between surfaces in mutual contact, which ultimately reduces the heat generated when the surfaces move. It may also have the function of transmitting forces, transporting foreign particles, or heating or cooling the surfaces. The property of reducing friction is known as lubricity. In addition to industrial applications, lubricants are used for many other purposes. Other uses include cooking (oils and fats in use in frying pans, in baking to prevent food sticking), bioapplications on humans (e.g. Lubricants for artificial joints), ultrasound examination, medical examinations.
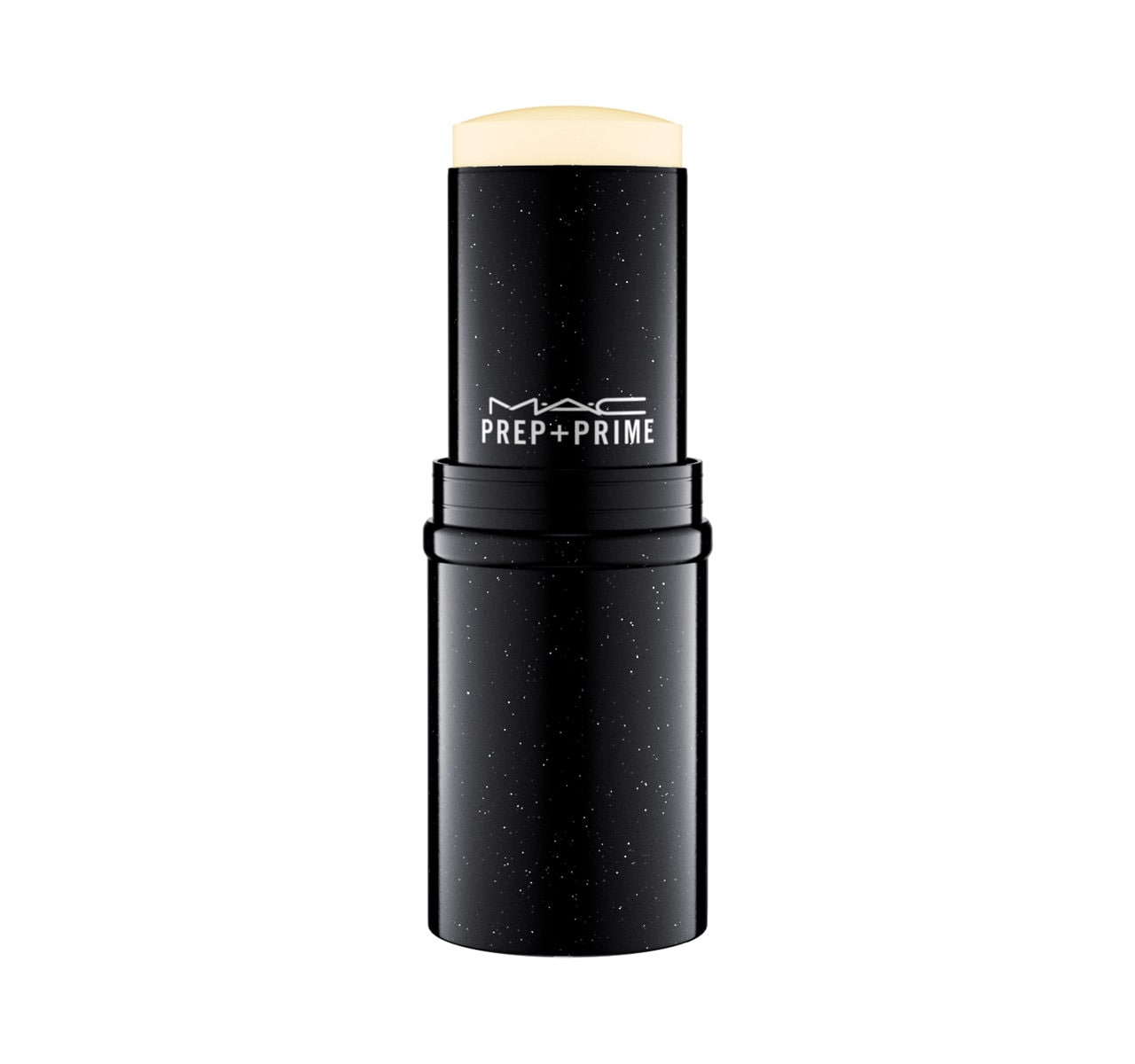
Formulation Typically lubricants contain 90% base oil (most often petroleum fractions, called mineral oils) and less than 10% additives. Vegetable oils or synthetic liquids such as hydrogenated polyolefins, esters, silicones, fluorocarbons and many others are sometimes used as base oils. Additives deliver reduced friction and wear, increased viscosity, improved viscosity index, resistance to corrosion and oxidation, aging or contamination, etc. Non-liquid lubricants include powders (dry graphite, PTFE, molybdenum disulphide, tungsten disulphide, etc.), PTFE tape used in plumbing, air cushion and others. Dry lubricants such as graphite, molybdenum disulphide and tungsten disulphide also offer lubrication at temperatures (up to 350 °C) higher than liquid and oil-based lubricants are able to operate. Limited interest has been shown in low friction properties of compacted oxide glaze layers formed at several hundred degrees Celsius in metallic sliding systems, however, practical use is still many years away due to their physically unstable nature.
Main article: Oil additive A large number of additives are used to impart performance characteristics to the lubricants. Modern automotive lubricants contain as many as ten additives, comprising up to 20% of the lubricant, the main families of additives are:. Pour point depressants are compounds that prevent crystallization of waxes. Long chain alkylbenzenes adhere to small crystallites of wax, preventing crystal growth. Anti-foaming agents are typically silicone compounds which lower surface tension in order to discourage foam formation.
Viscosity index improvers (VIIs) are compounds that allow lubricants to remain viscous at higher temperatures. Typical VIIs are polyacrylates and butadiene. Antioxidants suppress the rate of oxidative degradation of the hydrocarbon molecules within the lubricant.
At low temperatures, free radical inhibitors such as hindered phenols are used, e.g. butylated hydroxytoluene. At temperatures 90 °C, where the metals catalyze the oxidation process, dithiophosphates are more useful. In the latter application the additives are called metal deactivators. Detergents ensure the cleanliness of engine components by preventing the formation of deposits on contact surfaces at high temperatures.
Corrosion inhibitors (rust inhibitors) are usually alkaline materials, such as alkylsulfonate salts, that absorb acids that would corrode metal parts. Anti-wear additives form protective ‘tribofilms’ on metal parts, suppressing wear. They come in two classes depending on the strength with which they bind to the surface. Popular examples include phosphate estersand zinc dithiophosphates. Extreme pressure (anti-scuffing) additives form protective films on sliding metal parts.
These agents are often sulfur compounds, such as dithiophosphates. Friction modifiers reduce friction and wear, particularly in the boundary lubrication regime where surfaces come into direct contact. In 1999, an estimated 37,300,000 tons of lubricants were consumed worldwide. Automotive applications dominate, but other industrial, marine, and metal working applications are also big consumers of lubricants. Although air and other gas-based lubricants are known (e.g., in fluid bearings), liquid lubricants dominate the market, followed by solid lubricants.
Lubricants are generally composed of a majority of base oil plus a variety of additives to impart desirable characteristics. Although generally lubricants are based on one type of base oil, mixtures of the base oils also are used to meet performance requirements. Mineral oil The term “mineral oil” is used to refer to lubricating base oils derived from crude oil.
The American Petroleum Institute (API) designates several types of lubricant base oil:. Group I – Saturates 0.03%, and Society of Automotive Engineers (SAE) viscosity index (VI) of 80 to 120 Manufactured by solvent extraction, solvent or catalytic dewaxing, and hydro-finishing processes.
Common Group I base oil are 150SN (solvent neutral), 500SN, and 150BS (brightstock). Group II – Saturates 90% and sulfur 90%, sulfur. Main article: Dry lubricant PTFE: polytetrafluoroethylene (PTFE) is typically used as a coating layer on, for example, cooking utensils to provide a non-stick surface.
Its usable temperature range up to 350 °C and chemical inertness make it a useful additive in special greases. Under extreme pressures, PTFE powder or solids is of little value as it is soft and flows away from the area of contact. Ceramic or metal or alloy lubricants must be used then. Inorganic solids: Graphite, hexagonal boron nitride, molybdenum disulfide and tungsten disulfide are examples of solid lubricants. Some retain their lubricity to very high temperatures. The use of some such materials is sometimes restricted by their poor resistance to oxidation (e.g., molybdenum disulfide degrades above 350 °C in air, but 1100 °C in reducing environments.
Metal/alloy: Metal alloys, composites and pure metals can be used as grease additives or the sole constituents of sliding surfaces and bearings. Cadmium and Gold are used for plating surfaces which gives them good corrosion resistance and sliding properties, Lead, Tin, Zinc alloys and various Bronze alloys are used as sliding bearings, or their powder can be used to lubricate sliding surfaces alone. Aqueous lubrication Aqueous lubrication is of interest in a number of technological applications. Strongly hydrated brush polymers such as PEG can serve as lubricants at liquid solid interfaces.
By continuous rapid exchange of bound water with other free water molecules, these polymer films keep the surfaces separated while maintaining a high fluidity at the brush–brush interface at high compressions, thus leading to a very low coefficient of friction. Biolubricants Biolubricants are derived from vegetable oils and other renewable sources. They usually are triglyceride esters (fats obtained from plants and animals.

For lubricant base oil use the vegetable derived materials are preferred. Common ones include high oleic canola oil, castor oil, palm oil, sunflower seed oil and rapeseed oil from vegetable, and Tall oil from tree sources. Many vegetable oils are often hydrolyzed to yield the acids which are subsequently combined selectively to form specialist synthetic esters. Other naturally derived lubricants include lanolin (wool grease, a natural water repellent).

Whale oil was a historically important lubricant, with some uses up to the latter part of the 20th century as a friction modifier additive for automatic transmission fluid. In 2008, the biolubricant market was around 1% of UK lubricant sales in a total lubricant market of 840,000 tonnes/year. One of the single largest applications for lubricants, in the form of motor oil, is protecting the internal combustion engines in motor vehicles and powered equipment. Keep moving parts apart Lubricants are typically used to separate moving parts in a system. This separation has the benefit of reducing friction and surface fatigue, together with reduced heat generation, operating noise and vibrations. Lubricants achieve this in several ways. The most common is by forming a physical barrier i.e., a thin layer of lubricant separates the moving parts.
Specs fr roxio easy vhs to dvd for mac. This is analogous to hydroplaning, the loss of friction observed when a car tire is separated from the road surface by moving through standing water. This is termed hydrodynamic lubrication. In cases of high surface pressures or temperatures, the fluid film is much thinner and some of the forces are transmitted between the surfaces through the lubricant.
Reduce friction Typically the lubricant-to-surface friction is much less than surface-to-surface friction in a system without any lubrication. Thus use of a lubricant reduces the overall system friction.
Reduced friction has the benefit of reducing heat generation and reduced formation of wear particles as well as improved efficiency. Lubricants may contain additives known as friction modifiers that chemically bind to metal surfaces to reduce surface friction even when there is insufficient bulk lubricant present for hydrodynamic lubrication, e.g.
Protecting the valve train in a car engine at startup. Transfer heat Both gas and liquid lubricants can transfer heat. However, liquid lubricants are much more effective on account of their high specific heat capacity.
Typically the liquid lubricant is constantly circulated to and from a cooler part of the system, although lubricants may be used to warm as well as to cool when a regulated temperature is required. This circulating flow also determines the amount of heat that is carried away in any given unit of time.
High flow systems can carry away a lot of heat and have the additional benefit of reducing the thermal stress on the lubricant. Thus lower cost liquid lubricants may be used. The primary drawback is that high flows typically require larger sumps and bigger cooling units. A secondary drawback is that a high flow system that relies on the flow rate to protect the lubricant from thermal stress is susceptible to catastrophic failure during sudden system shut downs. An automotive oil-cooled turbocharger is a typical example. Turbochargers get red hot during operation and the oil that is cooling them only survives as its residence time in the system is very short (i.e.
Mac Nut Oil Sale
High flow rate). If the system is shut down suddenly (pulling into a service area after a high-speed drive and stopping the engine) the oil that is in the turbo charger immediately oxidizes and will clog the oil ways with deposits. Over time these deposits can completely block the oil ways, reducing the cooling with the result that the turbo charger experiences total failure, typically with seized bearings. Non-flowing lubricants such as greases and pastes are not effective at heat transfer although they do contribute by reducing the generation of heat in the first place.
Carry away contaminants and debris Lubricant circulation systems have the benefit of carrying away internally generated debris and external contaminants that get introduced into the system to a filter where they can be removed. Lubricants for machines that regularly generate debris or contaminants such as automotive engines typically contain detergent and dispersant additives to assist in debris and contaminant transport to the filter and removal. Over time the filter will get clogged and require cleaning or replacement, hence the recommendation to change a car’s oil filter at the same time as changing the oil. In closed systems such as gear boxes the filter may be supplemented by a magnet to attract any iron fines that get created. It is apparent that in a circulatory system the oil will only be as clean as the filter can make it, thus it is unfortunate that there are no industry standards by which consumers can readily assess the filtering ability of various automotive filters. Poor people significantly reduces the life of the machine (engine) as well as making the system inefficient. Transmit power.
Main article: Hydraulics Lubricants known as hydraulic fluid are used as the working fluid in hydrostatic power transmission. Hydraulic fluids comprise a large portion of all lubricants produced in the world. The automatic transmission’s torque converter is another important application for power transmission with lubricants. Protect against wear Lubricants prevent wear by keeping the moving parts apart. Lubricants may also contain anti-wear or extreme pressure additives to boost their performance against wear and fatigue. Prevent corrosion Many lubricants are formulated with additives that form chemical bonds with surfaces or that exclude moisture, to prevent corrosion and rust.
Mac Oil Control
It reduces corrosion between two metallic surface and avoids contact between these surfaces to avoid immersed corrosion. Seal for gases Lubricants will occupy the clearance between moving parts through the capillary force, thus sealing the clearance. This effect can be used to seal pistons and shafts.